Flow Meters
Introduction to Flow Measurement
A flow meter is an instrument used to measure linear, nonlinear, mass or volumetric flow rate of a liquid or a gas. When choosing flow meters, one should consider such intangible factors as familiarity of plant personnel, their experience with calibration and maintenance, spare parts availability, and mean time between failure history, etc., at the particular plant site. It is also recommended that the cost of the installation be computed only after taking these steps.
One of the most common flow measurement mistakes is the reversal of this sequence: instead of selecting a sensor which will perform properly, an attempt is made to justify the use of a device because it is less expensive. Those "inexpensive" purchases can be the most costly installations. This page will help you better understand flow meters, but you can also speak to our application engineers at anytime if you have any special flow measurement challenges.
One of the most common flow measurement mistakes is the reversal of this sequence: instead of selecting a sensor which will perform properly, an attempt is made to justify the use of a device because it is less expensive. Those "inexpensive" purchases can be the most costly installations. This page will help you better understand flow meters, but you can also speak to our application engineers at anytime if you have any special flow measurement challenges.

Learn more about flow meters
FLOW MEASUREMENT IN HISTORY
Our interest in the measurement of air and water flow is timeless. Knowledge of the direction and velocity of air flow was essential information for all ancient navigators, and the ability to measure water flow was necessary for the fair distribution of water through the aqueducts of such early communities as the Sumerian cities of Ur, Kish, and Mari near the Tigris and Euphrates Rivers around 5,000 B.C.Flow Measurement Orientation
The basis of good flow meter selection is a clear understanding of the requirements of the particular application. Therefore, time should be invested in fully evaluating the nature of the process fluid and of the overall installation.First Steps to Choose the Right Flow Meter
The first step in flow sensor selection is to determine if the flowrate information should be continuous or totalized, and whether this information is needed locally or remotely. If remotely, should the transmission be analog, digital, or shared? And, if shared, what is the required (minimum) data-update frequency? Once these questions are answered, an evaluation of the properties and flow characteristics of the process fluid, and of the piping that will accommodate the flow meter, should take place. In order to approach this task in a systematic manner, forms have been developed, requiring that the following types of data be filled in for each application: Download the Flow Meter Evaluation Form.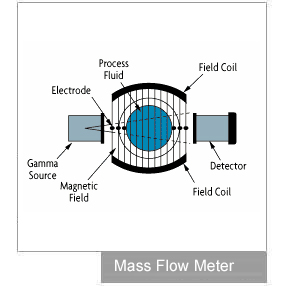
Fluid and flow characteristics
The fluid and its given and its pressure, temperature, allowable pressure drop, density (or specific gravity), conductivity, viscosity (Newtonian or not?) and vapor pressure at maximum operating temperature are listed, together with an indication of how these properties might vary or interact. In addition, all safety or toxicity information should be provided, together with detailed data on the fluid's composition, presence of bubbles, solids (abrasive or soft, size of particles, fibers), tendency to coat, and light transmission qualities (opaque, translucent or transparent?).Pressure & Temperature Ranges
Expected minimum and maximum pressure and temperature values should be given in addition to the normal operating values when selecting flow meters. Whether flow can reverse, whether it does not always fill the pipe, whether slug flow can develop (air-solids-liquid), whether aeration or pulsation is likely, whether sudden temperature changes can occur, or whether special precautions are needed during cleaning and maintenance, these facts, too, should be stated.Piping and Installation Area
Concerning the piping and the area where the flow meters are to be located, consider: For the piping, its direction (avoid downward flow in liquid applications), size, material, schedule, flange-pressure rating, accessibility, up or downstream turns, valves, regulators, and available straight-pipe run lengths. The specifying engineer must know if vibration or magnetic fields are present or possible in the area, if electric or pneumatic power is available, if the area is classified for explosion hazards, or if there are other special requirements such as compliance with sanitary or clean-in-place (CIP) regulations.KEY QUESTIONS TO ASK WHEN CHOOSING A FLOW METER
1. What is the fluid being measured?
2. Do you require rate measurement and/or totalization?
3. If the liquid is not water, what viscosity is the liquid?
4. Do you require a local display on the flow meter or do you need an electronic signal output?
5. What is the minimum and maximum flowrate?
6. What is the minimum and maximum process pressure?
7. What is the minimum and maximum process temperature?
8. Is the fluid chemically compatible with the flow meter wetted parts?
9. If this is a process application, what is the size of the pipe??
Flow rates and Accuracy
The next step is to determine the required meter range by identifying minimum and maximum flows (mass or volumetric) that will be measured. After that, the required flow measurement accuracy is determined. Typically accuracy is specified in percentage of actual reading (AR), in percentage of calibrated span (CS), or in percentage of full scale (FS) units. The accuracy requirements should be separately stated at minimum, normal, and maximum flowrates. Unless you know these requirements, your flow meter's performance may not be acceptable over its full range.In applications where products are sold or purchased on the basis of a meter reading, absolute accuracy is critical. In other applications, repeatability may be more important than absolute accuracy. Therefore, it is advisable to establish separately the accuracy and repeatability requirements of each application and to state both in the specifications.
When a flow meter's accuracy is stated in % CS or % FS units, its absolute error will rise as the measured flow rate drops. If meter error is stated in % AR, the error in absolute terms stays the same at high or low flows. Because full scale (FS) is always a larger quantity than the calibrated span (CS), a sensor with a % FS performance will always have a larger error than one with the same % CS specification. Therefore, in order to compare all bids fairly, it is advisable to convert all quoted error statements into the same % AR units.
In well-prepared flow meter specifications, all accuracy statements are converted into uniform % AR units and these % AR requirements are specified separately for minimum, normal, and maximum flows. All flow meters specifications and bids should clearly state both the accuracy and the repeatability of the meter at minimum, normal, and maximum flows.
Accuracy vs. Repeatability
If acceptable metering performance can be obtained from two different flow meter categories and one has no moving parts, select the one without moving parts. Moving parts are a potential source of problems, not only for the obvious reasons of wear, lubrication, and sensitivity to coating, but also because moving parts require clearance spaces that sometimes introduce "slippage" into the flow being measured. Even with well maintained and calibrated meters, this unmeasured flow varies with changes in fluid viscosity and temperature. Changes in temperature also change the internal dimensions of the meter and require compensation.Furthermore, if one can obtain the same performance from both a full flow meter and a point sensor, it is generally advisable to use the flow meter. Because point sensors do not look at the full flow, they read accurately only if they are inserted to a depth where the flow velocity is the average of the velocity profile across the pipe. Even if this point is carefully determined at the time of calibration, it is not likely to remain unaltered, since velocity profiles change with flowrate, viscosity, temperature, and other factors.
Mass or Volumetric Units
Before specifying a flow meter, it is also advisable to determine whether the flow information will be more useful if presented in mass or volumetric units. When measuring the flow of compressible materials, volumetric flow is not very meaningful unless density (and sometimes also viscosity) is constant. When the velocity (volumetric flow) of incompressible liquids is measured, the presence of suspended bubbles will cause error; therefore, air and gas must be removed before the fluid reaches the meter. In other velocity sensors, pipe liners can cause problems (ultrasonic), or the meter may stop functioning if the Reynolds number is too low (in vortex shedding meters, RD > 20,000 is required).In view of these considerations, mass flow meters, which are insensitive to density, pressure and viscosity variations and are not affected by changes in the Reynolds number, should be kept in mind. Also underutilized in the chemical industry are the various flumes that can measure flow in partially full pipes and can pass large floating or settleable solids.
Choose the right Flow Meter

The rotameter is a tapered tube and a float. It is the most widely used for for gases and liquids flow measurement because of its low cost, simplicity, low pressure drop, relatively wide rangeability, and linear output.

Piston-type flow meters use an annular orifice formed by a piston and a tapered cone. The piston is held in place at the base of the cone (in the "no flow position") by a calibrated spring. Scales are based on specific gravities of 0.84 for oil meters, and 1.0 for water meters. Their simplicity of design and the ease with which they can be equipped to transmit electrical signals has made them an economical alternative to rotameters for flowrate indication and control.

Thermal-type mass flow meters operate with minor dependence on density, pressure, and fluid viscosity. This style of flow meter utilizes either a differential pressure transducer and temperature sensor or a heated sensing element and thermodynamic heat conduction principles to determine the true mass flow rate. Many of these mass flow meters have integral displays and analog outputs for data logging. Popular applications include leak testing and low flow measurements in the milliliters per minute.

The ultrasonic doppler flow meters are commonly used in dirty applications such as wastewater and other dirty fluids and slurries which ordinarily cause damage to conventional sensors. The basic principle of operation employs the frequency shift (Doppler Effect) of an ultrasonic signal when it is reflected by suspended particles or gas bubbles (discontinuities) in motion.

The turbine meter can have an accuracy of 0.5% of the reading. It is a very accurate meter and can be used for clean liquids and viscous liquids up to 100 centistokes. A minimum of 10 pipe diameters of straight pipe on the inlet is required. The most common outputs are a sine wave or squarewave frequency but signal conditioners can be mounted on top for analog outputs and explosion proof classifications. The meters consists of a multi-bladed rotor mounted at right angles to the flow and suspended in the fluid stream on a free-running bearing.

One of the most popular cost effective flow meters for water or water like fluids. Many are offered with flow flittings or insertions styles. These meters like the turbine meter require a minimum of 10 pipe diameters of straight pipe on the inlet and 5 on the outlet. Chemical compatibility should be verified when not using water. Sine wave and Squarewave pulse outputs are typical but transmitters are available for integral or panel mounting. The rotor of the paddlewheel sensor is perpendicular to the flow and contact only a limited cross section of the flow.

These meters are used for water applications when no straight pipe is available and turbine meters and paddlewheel sensor would see too much turbulence. The positive displacement are also used for viscous liquids.

The main advantages of vortex meters are their low sensitivity to variations in process conditions and low wear relative to orifices or turbine meters. Also, initial and maintenance costs are low. For these reasons, they have been gaining wider acceptance among users. Vortex meters do require sizing, contact our flow engineering.

The pitot tubes offer the following advantages easy, low-cost installation, much lower permanent pressure loss, low maintenance and good resistance to wear. The pitot tubes do require sizing, contact our flow engineering.

Available in in-line or insertion style. The magnetic flow meters do not have any moving parts and are ideal for wastewater application or any dirty liquid which is conductive. Displays are integral or an analog output can be used for remote monitoring or data logging.

Hot wire anemometers are probes with no moving parts. Airflow can be measured in pipes and ducts with a hand held or permanent mount style. Vane anemometers are also available. Vane anemometers are usually larger than a hot wire but are more rugged and economical. Models are available with temperature and humidity measurement.